Making a Sleeve Board
When I started looking at commercially available boards I found many quite flimsy, with insufficient length to them.
The best I saw was a specialist Italian make, hardwood with a metal spring between board and base.
It came with quite a hefty price tag so I decided to copy the design and make one myself.
The board and it's base I made from 1" thick oak I already had and the the steel spring is made from 25mm by 6 mm steel strip, which likewise was already in my metal store. The board and base are secured to the spring using M8 countersunk head allen bolts into threads tapped directly in the metal spring strip.
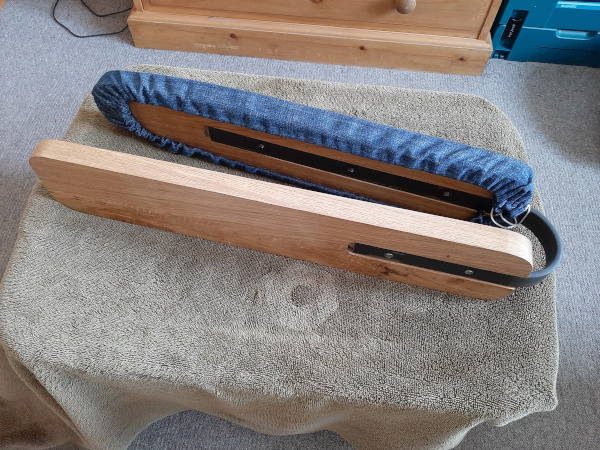
I bent the steel using a bending tool all I had made many years ago. You could do the same using a vice and a 4" bar or similar as a former, the essential thing is to get a clean curve without any kink which would become a weak spot in use.
The steel is bent about 165 degrees, leaving a shallow upwards tilt to the ironing surface which moves down to parallel when pressure is applied.
Not shown in these pictures which were taken shortly after it was made, I oiled the top and base section with tung oil, to protect against moisture absorption. This also gave an attractive darker finish.
The cover I made from some denim I had available and it is padded slightly using heavyweight paper type interfacing, which I found useless for sewing but seems to reflect heat quite well.
The result was aesthetically very pleasing and certainly makes it far easier now to press a seam completely flat when shirt or trouser making.
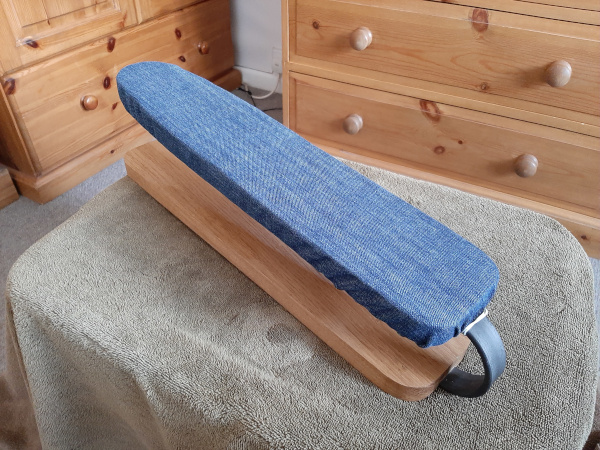